What is the difference between magnetoelastic, piezoelectric and multi-frequency ultrasound?
Its basic principle makes magnetoelastic ultrasound is one of the oldest ultrasound technologies. However, in the past it was very inefficient.
Piezoelectricity was discovered later and this is very cheap and is also imported cheaply from Asia. This explains why many manufacturers turned to piezoelectricity.
Magnetoelastic ultrasound
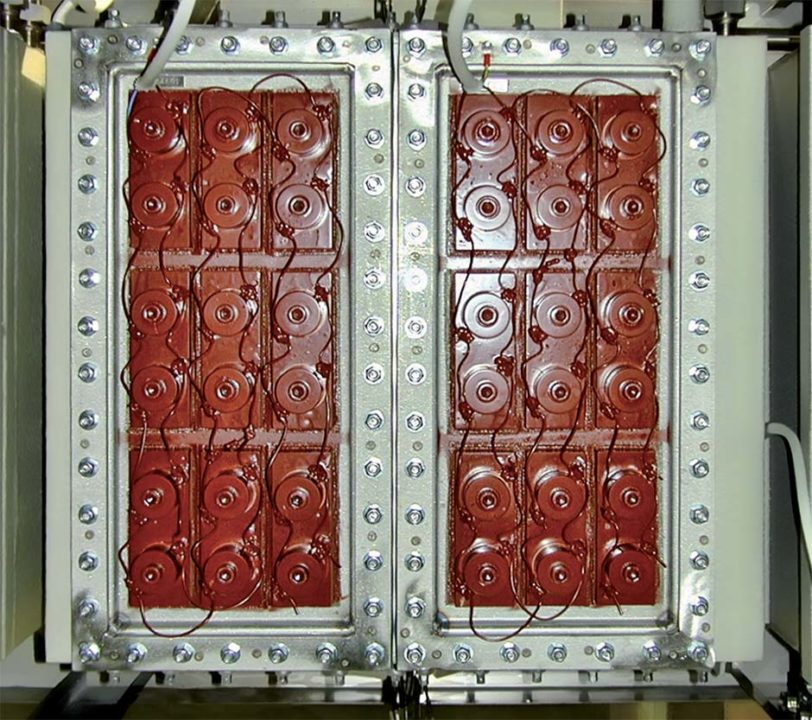
We have magnetoelastic ultrasonic cleaning systems that have been operating for 20 years without problems
However, we continued to work on magnetoelastic ultrasound, and we developed our Magnasonic ultrasound. It is much more efficient and above all, it almost never wears out, unlike piezoelectric emitters.
As a result, we have magnetoelastic ultrasonic cleaning systems that have been operating for 20 years without problems, and which still work today with the original ultrasonic emitter.
This is not possible with piezoelectric technology. In this field, the life span of emitters is generally between 4000 and 6000 hours.
This means that emitters have to be changed every one or two years, which does not apply to our magnetoelastic technology.
But you also use piezoelectricity
Yes, we use this technology when there are frequency requirements.
For example, in the component cleaning sector, we have machines that operate with multi-frequency or piezoelectric ultrasound. But magnetoelastic technology is better suited for cleaning molds and tools.
First of all, the temperatures for cleaning components are much lower:
- When cleaning molds, temperatures go up to 95 degrees,
- whereas components are usually cleaned at temperature of 40 to 50 degrees.
The problem with piezoelectric emitters is that they deteriorate very quickly at high temperatures.
A magnetoelastic ultrasonic system can be used above 100 degrees and still would not wear out. Long operating times are also possible with magnetoelastic ultrasound.
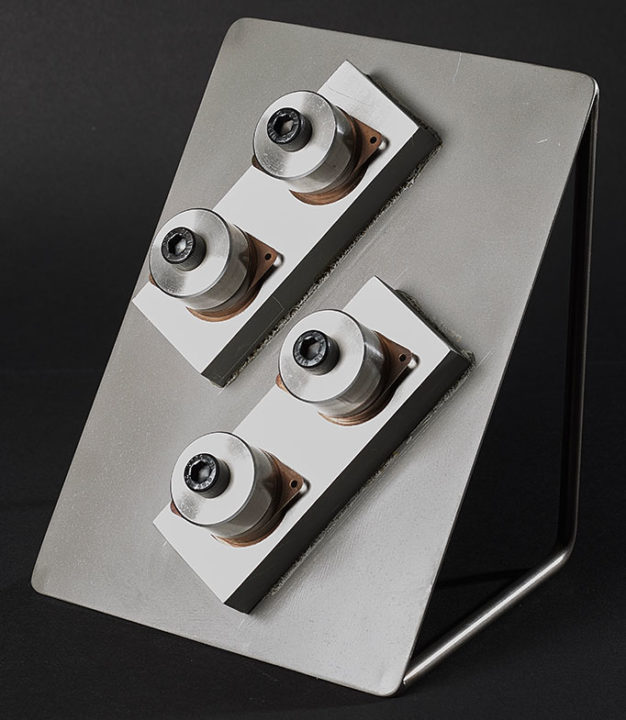
So we have very different operating times and temperatures in different sectors
If you clean a medical part, you may wash it for up to two or three minutes. If you are cleaning a permanent mold used in a foundry, it may take up to an hour.
So we have very different operating times and temperatures in different sectors.
So magnetoelastic technology has many advantages for mold cleaning. It can be used at high temperatures and for long operating periods without the emitter wearing out. Are there any other advantages? What makes magnetoelastic ultrasonic cleaning especially suitable for molds and tools?
Magnetoelastic ultrasound uses very low frequency ultrasound. In general, the ultrasound frequency range in the tanks is between 18 and 20 kHz.
In addition – and this is also important – we modulate the frequency continually between 18 and 20 kHz. This means we don’t generate standing waves.
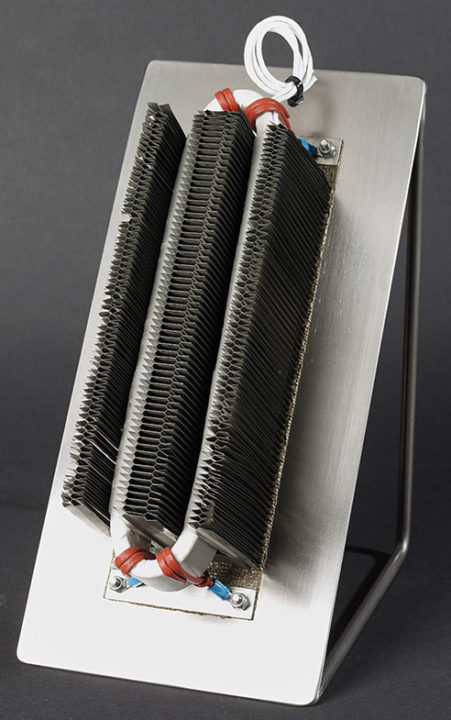
Magnetoelastic ultrasound uses very low frequency ultrasound
Standing waves
A standing wave is like a sine wave, which starts from a point A and goes to a point B. It will always arrive at the same point – and that is precisely what we want to avoid.
I’ll give you an example: If you rub a diamond with a piece of wood, people will tell you that nothing can happen.
But if I always rub my piece of wood in the same place on the diamond, at some point I’ll end up noticing wear.
Standing waves cause cavitation damage. Surfaces are eroded.
To avoid this, we modulate the Magnasonic ultrasound frequency between 18 and 20 kHz.
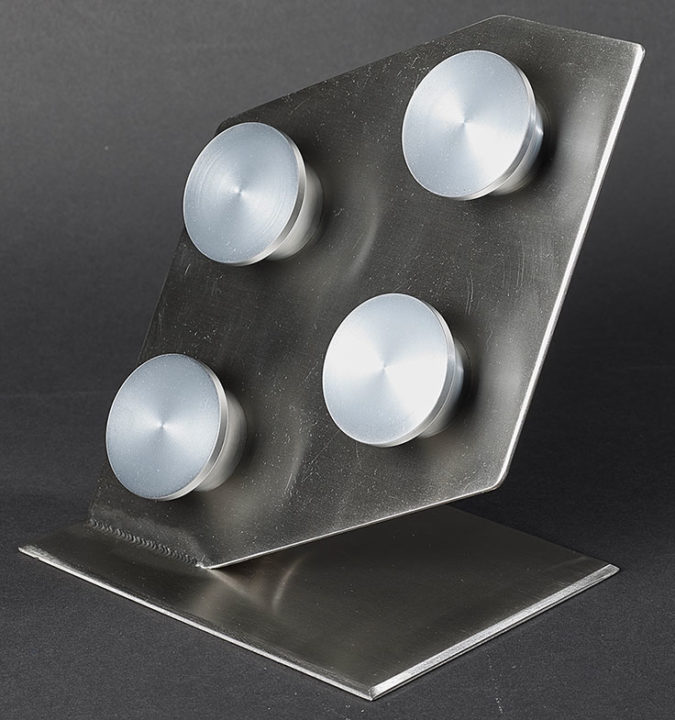
Standing waves cause cavitation damage
Very large bubbles for thorough cleaning of heavily soiled surfaces
The low frequency also has another advantage: because we are using very low frequencies, we generate very large bubbles.
What does a large bubble mean? A large bubble contains a lot of energy. These bubbles appear in the liquid and when they meet the surface, they implode, forming very violent liquid micro-jets that scrape off the dirt.
Using higher frequencies generates smaller bubbles and they are less efficient for cleaning. Because we have large bubbles, we can clean heavily soiled surfaces relatively well.
FISA, 22 marca 2020
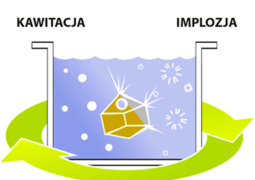